Quality Management Evolves From Function To Culture Of Bio/Pharmaceutical Businesses
By Samantha Atkinson, executive vice president and principal consultant, NSF
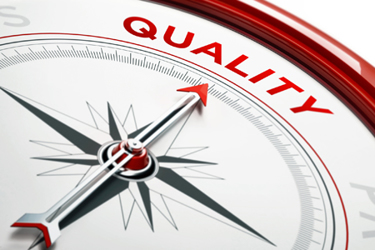
Quality management maturity (QMM) has been forecasted as a new trend in the pharmaceutical industry, lauded as the latest evolution in quality management system (QMS) and, as recently as September 2023, enshrined in the FDA’s regulatory documents as a defined assessment protocol.
However, none of these monikers encapsulate all that QMM offers to pharmaceutical manufacturers, contractors, brands, suppliers and, most importantly, patients. In totality, QMM is a state of operation that creates a culture of quality to ensure business continuity, builds consumer and industry trust, and creates clear regulatory pathways to compliance. Effectively deployed, it results in high performance, lower levels of noncompliance, and reduced supply disruptions.
Continued Challenges With QMS Have Led To Drug Shortages
In 2019, a U.S. Federal Drug Shortages Task Force was convened to identify and provide solutions to the issue of drug shortages in the U.S. One of the three root causes of shortages noted by the authors of the report was that the market failed to recognize and reward manufacturers for mature quality management systems. In fact, the report concluded 62% of shortages between 2013 and 2017 were attributed to manufacturing or product quality problems. Despite the evidence that nearly one-third of drug shortages resulted from quality issues, manufacturers were more likely to keep costs low and seek to meet only the minimum requirements of current good manufacturing practices (cGMPs). Because manufacturers are not incentivized to enhance the maturity of their quality systems beyond the bare minimum mandate, manufacturing practices are susceptible to quality issues resulting in shortages.
This problem is not specific to the U.S.; since at least 2015, quality systems have been the subject of the highest number of deficiencies for the Medicines and Healthcare products Regulatory Agency (MHRA) in the U.K.
In response to the task force’s report, CDER proposed a five-level rating system to assess QMM at a manufacturer’s facility. In this way, the industry’s long-held tradition of operating under a QMS gave rise to the idea of QMM, as enacted by the rating system, to measure robustness and performance.
QMS: No Longer A Checklist But The Heart And Lungs Of An Organization
Historically, QMS has been managed as a function by a dedicated team with a comprehensive set of instructions. The outcome has been that although QMS is the focus of regulatory inspections and the cause of many findings, it remains an area of noncompliance across many organizations.
As this trend has borne out over the past few decades, we have seen regulators, quality professionals, and the industry shift the collective thinking about QMS from ink and paper – in the form of checklists and event reporting — to a framework that sees QMS embedded as the heart and lungs of an organization.
In this allegory, QMS both breathes life into the organization by future-proofing quality and supporting supply chain robustness and pumps information and guidance to each operational part of the enterprise, like a heart sending blood to each extremity.
This shift in mindset also considers the impact, and risk, people and culture play in the successful deployment of a mature QMS. Individuals, technology, equipment, functions, teams, and processes must be united in their understanding of QMM and their responsibility to co-create a culture of quality.
Nowhere is this shift more evident than in the FDA’s new document, CDER’s Quality Management Maturity Program: Practice Areas and Prototype Assessment Protocol Development.
Indeed, many now agree that QMM is no longer seen as the responsibility of a team – it is now considered a more holistic function, composed of both the visible and invisible attributes of processes. QMM, in short, is not just what is “in place” and “in use,” but what is happening “in reality.”
FDA Places Quality Maturity Management In Center Stage
According to the FDA, “QMM is the state attained when drug manufacturers have consistent, reliable, and robust business processes to achieve quality objectives and promote continual improvement.” The FDA also has alluded to the fact that QMM considers “manufacturers and those with oversight and controls over manufacturing” to take ownership of quality, including “the tone of commitment to quality” and the fact that “quality systems shape culture.”
Teams operating in a culture imbued with a QMM mindset identify and anticipate deficiencies, which are then quickly investigated and resolved. Impacts are managed and future risks are mitigated using effective feedback loops to inform ongoing activities.
A level of cohesion this smooth requires an enhanced state of quality culture and a different approach — looking at the organization through a new lens, understanding the employees within, creating alignment to drive behavioral changes, motivating and incentivizing individuals toward quality deliverables, and assessing effectiveness and robustness, alongside compliance — all leading to a positive quality culture. At its apex, it requires unwavering dedication by organizational leadership and a high degree of alignment and trust, leading to improved risk management and enhanced compliance.
Much work has been undertaken not just to consider quality culture but the “quality climate” of an organization, where dimensions such as safety climate, innovation climate, learning climate, ethical climate, and inclusion climate are explored to determine the impact and influence of behaviors on an organization’s culture. Understanding both the culture and the climate enables an organization to better shape the future culture.
However, cultural change is hard to undertake and even harder to measure. It is therefore imperative that an organization pins down exactly what it needs and wants to change. Key to leveraging the greatest level of change is the understanding of early indicators and longer-term measures.
When we ask how QMM can give breath and blood to organizations and how regulators can assess the impact of intangible elements like culture, tone of commitment, and inclusion climate on the effectiveness and robustness of QMS, what we’re really asking is, “what is QMM, how does it work, and how can it be used to bridge cultures and create a more cohesive organization focused on quality?”
This is the first in a series of three articles about quality management maturity. The first article covers the history and context of QMM, setting the stage for an in-depth discussion; the second will delve into how QMM bridges cultures and breaks down barriers, focused on emerging markets; and the third will share a case study to highlight data on cost of quality and impact on quality systems.
About The Author: