5 Best Practices For Responding To FDA Form 483 Inspection Observations
By Susan Shockey, Clarkston Consulting
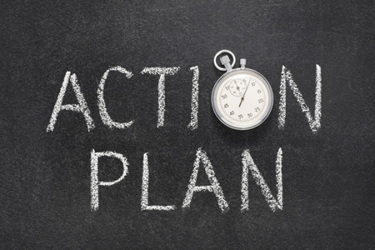
FDA inspections, whether pre-approval inspection (PAI), bioresearch monitoring (BIMO),1 or routine, are important steps as you move forward in the life cycle of your pharmaceutical product. During an FDA inspection, any issues observed by the inspectors will be documented on an FDA Form 483.2 The observations are identified based upon risk that there are suspected specification non-conformances that may indicate a product is unfit or unsafe for use.
How you respond to the observations will determine if they escalate into more serious consequences, such as a warning letter or enforcement action. A review of published warning letters confirms that a significant percentage could have been avoided by a proper response to the Form 483. Our goal is to help you take appropriate actions to optimize the outcome after receipt of FDA observations.
The following steps will guide your actions toward an optimal response to FDA Form 483 inspection observations.
1. Understand The Observation
The most important first step is to ensure that you understand the documented observation. During the inspection, it’s important to clarify any discussion between the investigator and the identified subject matter expert (SME) in order to ensure the investigator has an accurate understanding of the situation. If needed, you can pause the discussion to consult with other SMEs and collect any evidence of compliance. The daily wrap-up is then your opportunity to ensure you understand the identified compliance gap.
At the inspection close-out meeting, the inspector will provide a summary of all observations noted. It’s important to get clarification from the inspector to ensure all observations are fully understood so appropriate actions can be taken. If an observation has been corrected during the course of the inspection, you should present any objective evidence of the implemented corrective action, as it may be accepted by the inspector at that time, which will result in closing out the observation.
2. Investigate The Findings
After the inspectors have left, it’s time to address any inspection findings. It's important to take the observations seriously — if it was critical enough for the FDA to document, it needs to be corrected. Some FDA Form 483s are written with “boilerplate” language that may not describe the true concerns. Additional research into the context of the observations may be needed in order to accurately define the identified compliance gap and articulate the problem statement.
After your problem statement is formulated, you can start the investigation into the root cause and determine the appropriate corrective actions. Be sure to document the scope of the investigation, the root cause analysis tools used in the investigation, and the outcome of the investigation. For each observation, clearly identify the root cause and the corrective and preventive actions needed.
The patient safety implications of an observation are critical to the FDA. Product and patient impact, including evaluation of the safety, identification, strength, purity, and quality of the product, must be addressed. Fully document the investigation methods used, the outcomes of those investigations, the results of the impact analysis, and any actions taken.
While immediate corrections may have been taken to address the specific situation, it’s also necessary to identify any additional actions needed to prevent recurrence. It’s critical to expand the investigation beyond the immediate focus to ensure similar risk areas are addressed. You need to look for systemic issues that could be contributing factors. With this preventive action mindset, review for similar gaps in other systems — look at a longer time span, other products using the same systems, and any similar processes in other quality systems. If systemic factors are identified, additional actions are needed to address these related root causes.
Additionally, it’s necessary to evaluate the need for product actions on impacted products and impacted lots based on the identified issues. Determine if you need to investigate other lots of product that could potentially be affected by the cited nonconformance. If product actions are necessary, they may involve putting quality holds on current inventory, both on-site and in distribution.
3. Develop A Corrective And Preventive Action (CAPA) Plan
The next step is to document all planned corrective and preventive actions in an overall CAPA plan. The CAPA plan will be used to document your intended actions and demonstrate progress along the way, as well as report closure when the individual actions have been completed. The CAPA plan will address implementation of true solutions that are achievable in a realistic time frame. It should also address correction of the specific issues noted, as well as any identified systemic issues. For any actions that cannot be immediately completed, provide a detailed explanation, a mitigation plan, and a time frame for completion.
Implementation of the CAPAs may require change controls to revise SOPs, develop new SOPs, and validate or revalidate test methods, processes, and systems. Ensure any required training is identified as part of the change, and that training is completed before implementing the changes.
Actions may take a significant time to fully implement, so developing a mitigation plan will identify actions to be taken to ensure compliance until the permanent solutions are in place. This plan should identify interim controls, such as additional manufacturing controls, process monitoring, in-process testing, or release testing. The CAPA plan should also include focused and measurable effectiveness checks to verify that the actions taken have had the intended impact to resolve the identified issues. You may want to consider using experts who have not been involved in the investigation for an objective perspective on the results.
4. Respond To The FDA
The FDA requires a preliminary response to the Form 483 within 15 working days. If the Form 483 is extensive, it’s acceptable to respond in the 15-day window by asking for an extension in order to provide a complete and detailed response.
It’s critical to ensure that your CAPA plan is well-defined. Address each observation individually, and include any related systemic issues identified. Be sure to also include detailed documentation of the investigation process, the root cause investigation tools used, the outcome of the investigation, and the CAPAs identified. Provide a complete description of the actions already taken to immediately correct issues, along with objective evidence of completion. If additional time is needed for further investigation, or for implementation of CAPAs, provide target dates for completion.
You’ll also need to track progress of the CAPA plans very closely and prepare periodic follow-up letters to the FDA until all CAPAs are reported closed. For ongoing actions, provide a description of work completed to date and realistic expected completion dates for remaining work. Explain any delays on pending actions and what was done to mitigate their impact. Also include and explain any new information discovered. As actions are completed, be sure to provide evidence of changes made, documents updated, and training conducted.
5. Follow Up And Prepare For Future Inspections
As the identified observations are being addressed, you want to document the investigation process and maintain a record of how the observations have been addressed. Be sure to put together a package containing the list of observations, the investigation plans and findings, the root causes identified, the CAPAs implemented, and objective evidence of all actions taken so it’s ready for review at your next inspection.
It’s important to monitor your quality systems for similar issues and concerns in the future, as repeat findings during your next FDA inspection will likely result in a warning letter. I also recommend that you review the FDA’s top cited observations on the FDA website.3 The observations will identify the hot topics the FDA is looking at so that you can ensure you’re prepared.
Properly Addressing FDA Form 483 Inspection Observations
While it can be unnerving to receive an FDA Form 483 at the end of an inspection, following these steps will ensure that the findings are properly addressed. In addition, this can be used as an opportunity to not only correct the identified issues but also uncover related issues and correct them to improve your overall quality system.
Also, the FDA is holding a webinar, Understanding FDA Inspections and Data, on September 6.
References
- Shockey, S. (2022, October 26). What Your Company Needs to Know About Preparing for an FDA Inspection. Clarkston Consulting. https://clarkstonconsulting.com/insights/preparing-for-an-fda-inspection/
- Lee Jones, L. (2022, August 17). How to Avoid Form 483s for Biopharma Software Validation Failures. Outsourced Pharma. https://www.outsourcedpharma.com/doc/how-to-avoid-form-s-for-biopharma-software-validation-failures-0001
- U.S. Food and Drug Administration. (2022, November 11). Inspection Observations. https://www.fda.gov/inspections-compliance-enforcement-and-criminal-investigations/inspection-references/inspection-observations
About The Author:
Susan Shockey is a director with Clarkston Consulting and has wide-ranging experience in quality and regulatory compliance. She has 18 years in the life sciences area, focusing on quality systems, quality process improvement, and inspection preparation and remediation. Prior to that, she spent 15 years in quality assurance engineering supporting manufacturing, testing, and validation of NASA space flight and military hardware.