CGMP Requirements For Automated Facility Monitoring Systems
By Tim Sandle, Ph.D.
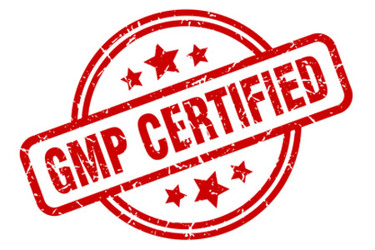
In pharmaceuticals and healthcare, “facility” refers to the operational space, such as a cleanroom. The critical controls that maintain the facility are delivered through key utilities like air handling systems. To assess facility control, most organizations use facility monitoring systems (FMSs) to monitor the manufacturing workspaces continuously. Such systems are designed to be always on when the facility is in the operational state, ensuring compliance with important parameters across identified ranges. An important element for microbiological control is particle counting, which verifies the class of the cleanroom and indicates how well control is being maintained. Interconnected devices provide continuous monitoring of facilities, including aseptic and controlled environments. Other environmental data is also of importance for the contamination control strategy, including temperature, humidity, air velocity, and pressure. The design of these automated environmental monitoring systems should be based on quality risk management principles.1
FMS design should take the following into account:
- product quality and product safety requirements
- regulatory requirements
- the needs and constraints imposed by equipment and processes
- the contamination control strategy concept adopted in the facility
- health and comfort of personnel
Such systems monitor the status of a facility through the use of a combination of fixed and portable instruments, including those for measuring viable and non-viable particles, as well as other environmental sensors. The instruments and their collected measurements come together as an industrial architecture design, combining IT hardware and processors with a range of software options for data capture, data analysis, data security, and system availability.
Facility Monitoring Systems
FMSs are sometime broken down into a subsystem called the environmental monitoring system (in other cases the assessment of particles is part of the overall system). In turn, the FMS is normally connected to but independent from the wider building management system. Here, there is a distinction between the FMS being a cGMP system and the building management system containing GxP and non-GxP elements.
FMSs are designed to monitor, record, and display environmental parameters and compare the measured values against fixed alarm limits. Typically, this is via a simple user interface capable of showing alarm states displayed on mimic diagrams of simplified floor plan(s) of the facility.
The system should comprise a real-time, multitasking software environment that allows a number of separate tasks to be performed simultaneously. This will include a real-time database for each measured parameter that holds its analog value and alarm programming. To support data acquisition there will need to be a number of standard software modules configured to perform the tasks required, including input-output (I/O) subsystem drivers, data logger, alarm logger, and an audit logger (the latter being a critical piece of functionality to meet data integrity expectations). The operating system should also be user friendly, in the form of a human-machine interface that allows the users to connect with the system via a point and click graphical user interface.2
Total Particle Counting
All FMSs will include a particle counting function.3 This is typically in the form of discrete particle counters collecting data continuously. The types of discrete particle counters attached will be those that can provide a total particle count; some systems can accommodate more sophisticated counters that can provide both the total particle count and a secondary count of microbial-carrying particles,4 based on spectrophotometric analysis.
In terms of conventional laser particle counters designed to provide the total particulate count, these contain a laser diode that generates a narrow beam that is focused and aligned so that it passes through the air being drawn through the counter chamber. A light detector is mounted at an angle to the beam. As a particle passes through the beam, light is scattered and reflected to the detector. The detector collects the light and represents it as a current value.
An electronic circuit then generates a voltage from the current value received. Larger particles scatter more light, thereby generating a greater voltage. The voltage level from the detector is compared against the preset (calibrated) threshold level for each channel size. Electronics within the counter then count the voltage pulses at each comparator to produce the counts for preselected particle sizes. Air is drawn through the counter at a preset rate (such as 1 cubic foot per minute).
The system software will then seek to normalize the result to counts per cubic meter (as required by U.S. and European regulatory agencies). This should not be done by simply multiplying up the count for a cubic foot to express it as a cubic meter as this distorts data that is not normally distributed. Most systems either simply count the particles in a discrete 36 x 1 minute sample set to estimate the total per cubic meter or gather a “rolling window” of samples, where each new 1-minute sample replaces the first 1-minute sample particle value in the calculation.
Irrespective of the particle counter model, the following are the minimum requirements:
- Type of particle counters
- The particle counter selected must be capable of continuous monitoring for a period greater than its service or calibration frequency (that is, six-months or one year).
- The particle counter must be compatible, in terms of remote control and with data acquisition, with the FMS. Counters can either be wired into a computer network or have wireless functionality. The advantage of the latter is greater portability, provided that the Wi-Fi signal can be maintained.
- Counting mode
- cGMP calls for the particle counts to be reported in cumulative count mode; that is, the particles reported as being ≥0.5 micron should include all particles ≥0.5 micron, including those ≥5.0 micron.
- Location of particle counters
- Particle counters must be located in representative areas in relation to the process being monitored and in locations that have been assessed as “worst case” (based on cleanroom classification data; cleanroom design data, such as airflows and air patterns; or by risk assessment, considering people and process flows).5
- When selecting a location, it is important to ensure that the particle counter tube length is 1 meter or less and that any bends are minimized, and that the radius of the bend exceeds 15 centimeters (these factors help to minimize the dropout of larger particles and, hence, underestimating the total airborne count).
- Vacuum control panels are required to provide vacuum to the particle counters. It is important that each particle counter is served by a separate vacuum control valve so that a failure of one counter does not impact the others that form the network. An area of weakness with many FMSs is a decrease in pump capacity or pump failure. A backup pump system can help safeguard against this occurrence.
- Calibration of particle counters
- Particle counters must be calibrated against a recognized standard, such as ISO21501.
- Ensuring suitable particle counter flow rate
- This is important in order to avoid under-representative sampling.
- Communication between particle counters and the software
- This is essential to avoid data loss.
- To support data acquisition, there needs to be verification of data capture.
- Data analysis
- Trend analysis is particularly important, especially for assessing area performance.
- Trend graphs, tabular reports, and alarm reports based on the measured parameters are normally accessed via password control.
Some FMSs also have the capability to control, and to collect data for, active air samplers. These are often in the form of aluminum or stainless-steel heads contained within a barrier system (such as a RABS or an isolator) and where the main body of the sampler is contained outside in order to minimize particle generation and retention. Flow rates, sample volumes, and run times can be controlled by the FMS software.
Other Functionality
In addition to the particle counters, sensors will need to be fitted in each area, taking into account the optimal locations, to deliver the combined measurement of temperature and relative humidity. For pressure, there are different forms of sensors and gauges. One common type is a pressure transducer, which uses force to calculate pressure, transforming deformation into an electrical signal.
Alarm Setpoints And Real-Time Assessments
For both particle counting and other environmental parameters, such as pressure and humidity, it is important that appropriate alarm setpoints are used and that data is responded to in real time (especially during pharmaceutical processing). For a new facility, initial data can be evaluated to determine the appropriate alarm requirements to serve as alerts, with regulatory set levels acting as action levels. Alert levels can be reviewed as more experience with the facility is gained. In the operational state, it is important that parameters that go into alarm state are responded to and that measures are taken to safeguard product.
Data Controls
For data security and to help to maintain data integrity, the system should be protected from unauthorized access by requiring the entry of a username and password. Administrator access should be in place to prevent inadvertent modification of system parameters and to restrict certain facilities to those authorized to access them.
A further element of data protection is the ability of the system to continue to log and record data in the event of a network failure.
Safeguards
As FMSs are critical for verifying cleanroom controls and for collecting data relating to the environment within which the dispensing of products occurs, having safeguards in place to prevent data loss is an important additional feature. One such safeguard is so-called “hot standby architecture.” This is a secondary system in the form of a standby server that can continuously monitor the health of the primary server. The standby server should automatically take over the FMS’s functionality (such as data monitoring and data logging) in the event of a failure of the primary server. This is achieved by using system watchdog devices, one each for the primary and standby servers. These are cross-wired to each other, allowing failure of one server to be detected by the partner server.
Another form of safeguard is the provision of an uninterruptible power supply unit that can provide mains conditioning and backup for the FMS’s server computers, the vacuum control panels, and the vacuum pump.
References
- Sandle, T. (2011): ‘Risk Management in Pharmaceutical Microbiology’ in Saghee, M.R., Sandle, T. and Tidswell, E.C. (Eds.) (2011): Microbiology and Sterility Assurance in Pharmaceuticals and Medical Devices, New Delhi: Business Horizons, pp 553-588
- Martinez, Wendy L. (2011) Graphical user interfaces: Graphical user interfaces. Wiley Interdisciplinary Reviews: Computational Statistics. 3 (2): 119–133
- Sandle, T. (2013). Contamination Control: Cleanrooms and Clean Air Devices, Encyclopedia of Pharmaceutical Science and Technology, Fourth Edition, Taylor and Francis: London, pp634 – 643
- Whyte W, Green G and Whyte W M: (2012) Removal of Microbe-Carrying Particles by High Efficiency Air Filters in Cleanrooms, International Journal of Ventilation, 10(4), pp 339-351
- Whyte W, M Hejab, WM Whyte and G Green: (2012) Studies of airflow in a cleanroom with respect to air supply inlets, Clean Air and Containment Review, Issue 10, pp 4-9
About The Author:
Tim Sandle, Ph.D., is a pharmaceutical professional with wide experience in microbiology and quality assurance. He is the author of more than 30 books relating to pharmaceuticals, healthcare, and life sciences, as well as over 170 peer-reviewed papers and some 500 technical articles. Sandle has presented at over 200 events and he currently works at Bio Products Laboratory Ltd. (BPL), and he is a visiting professor at the University of Manchester and University College London, as well as a consultant to the pharmaceutical industry. Visit his microbiology website at https://www.pharmamicroresources.com.