Green Gains In Biopharma Without Closing Facilities?
By Geoff Weiss, Custom Chromatography Research
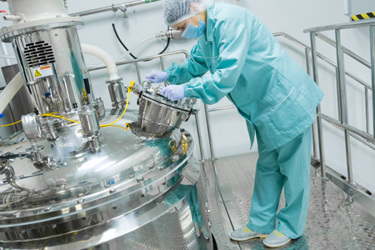
Discussions about sustainability improvements in biopharma usually center on single-use technology (SUT) and traditional stainless-steel equipment. This idea, however, is usually a non-starter for established facilities, as the cost and complexity of changing formats in legacy manufacturing environments are significant.
There are, however, opportunities for existing facilities to reduce their carbon footprint and environmental impact without significant disruptions to operations, quality systems, or regulatory status, creating both immediate and peripheral competitive advantages. These opportunities include using a hybrid SUT or stainless-steel approach, stakeholder education, monitoring and tracking energy use and waste generation, analyzing and modifying energy-intensive operations, and seeking site-specific adaptations of new technologies.
Single-Use Vs. Stainless Steel
A hybrid approach or phased transition might be the best practice for clinical- and commercial-stage companies with validated processes. Plant designers and operators love the benefits of SUT, including lower capital costs, eliminating clean-in-place (CIP) and sanitization-in-place (SIP) and validating those steps, improved process flexibility, and faster turnaround times.
From a sustainability perspective, however, SUT may be less attractive. The large amount of solid waste generated is a significant, perceptual, and real problem. A 2015 study determined that laboratories generate 2% of total global plastic waste. In addition, producing and transporting consumables has a considerable carbon cost.
The sustainability problems with SUT are somewhat offset by the reduction in energy, water, and chemicals needed for CIP/SIP required by a stainless-steel plant.
The solution that may make the most sense in validated environments is implementing a hybrid approach focusing on changes that could improve sustainability while minimizing disruptions to existing operations. One example is using SUT for operations at high risk for contamination when CIP/SIP is challenging to validate, such as in bioreactor operations. In contrast, buffer preparation, a step that is both lower risk and has a reduced validation requirement, may be performed satisfactorily using stainless steel. Another hybrid solution example is the potential for cleaning and reusing single-use components when appropriate.
Educating Stakeholders
As with any company-wide directive, the sustainability initiative should be thoughtfully conceived and constructed using cross-functional teams and honest commitment at the executive level to ensure the greatest probability of success. Clear, science-driven communication to R&D staff, plant operating personnel, purchasing agents, facilities engineers, vendors, etc., must be used to establish that reducing the organization’s carbon footprint and waste is a priority and company-wide objective. Most agree this is a worthy goal, but defined programs with metrics and incentives will empower employees and accelerate results.
Formal initial training, regular management updates, and brown-bag roundtables are just a few ways to advance goals and keep the topic front of mind. Innovations and refinements to best practices and SOPs by lab personnel can be benchmarked and drive compliance with corporate directives, creating scientific successes and gains as well as favorable publicity opportunities. For example, lab redesign and remodeling to LEED (Leadership in Energy and Environmental Design) design and construction standards improve the facility directly via healthy, highly efficient, and cost-saving green buildings while also providing environmental, social, and governance benefits to the company/organization that can be leveraged to drive positive public affairs and increase recruiting/retention, to maximum benefit.
Monitoring And Tracking
Measuring is the first step in reducing energy use and waste generation. Adding in-line sensors to distributed energy users is an excellent way to pinpoint areas for improvement.
HVAC and electrical plug load are two major end users of power that should be monitored and tracked separately. Purchasing of SUT consumables and other items contributing to waste streams should be tracked, and those costs should be reviewed and analyzed.
Cleanroom Air
The highest energy user in a biopharma production facility is the electricity to power cleanroom utilities. Because of the unique requirements for cleanroom air, the HVAC loads per square foot can be greater than 10 times higher than in commercial office buildings. Opportunities to reduce carbon footprint are plentiful. An initial energy audit will pinpoint opportunities to achieve energy savings.
Consider simple efforts such as shutting down complete HVAC when unnecessary or lowering excessive air change rates. For example, a 10% airflow reduction results in 28% less fan power consumption.
Significant efficiency gains can be achieved by replacing or retrofitting legacy equipment and control systems. Reducing the cleanroom background requirements might be possible by using closed downstream processes. Again, cross-functional teams must be involved in designing, analyzing, and selecting improvements to this multifaceted environment. Reduced ongoing costs for energy needs and HR/publicity benefits will offset the line-item cost of implementing these changes.
New Technologies
As global sustainability becomes more accepted and less debated, innovation outside of biotechnology continues concurrent with our own developments. Scientists must stay abreast of innovations in other industries designed with sustainability and reduction of environmental impact in mind and be prepared to incorporate these in our laboratories and facilities when appropriate. Some relevant examples might include:
- Use cleaner and renewable energy sources, such as electricity, instead of fossil fuels. Utilize energy generation sources that include solar, wind, or nuclear.
- Select materials that are more readily reusable or easily recyclable. One of the biggest sustainability problems with SUT is the large amount of plastic waste, often decontaminated using heat or chemicals and then sent to landfills, resulting in that 2% of global plastic waste. Decontamination often renders the plastic unusable for recycling, and many materials used currently are unsuitable for reuse. Research is ongoing to solve this problem with materials that can be more easily recycled. Pilot studies are also underway to test ways of reclaiming energy from plastic waste.
- Encourage employee engagement with and ownership of the directive via incentive-driven opportunities to suggest, analyze, and implement process innovations. What might seem minor or insignificant could generate significant savings. Remember, there’s no such thing as a bad idea!
About the Author:
Geoff Weiss is a consulting process scientist with over 30 years of biopharma experience at the lab bench and in the boardroom with both developing and Fortune 1000 companies. The Lehigh University graduate has consulted and traveled throughout the world independently and as an employee delivering laboratory process improvements. He works and lives in the San Francisco Bay Area.