Lessons Learned Executing A Closed Connected Process From Start To Finish
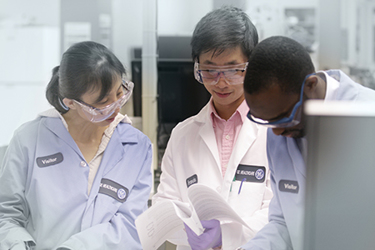
Biomanufacturing is under increased pressure to adapt to market demands, such as reducing costs and bringing life-saving therapies to the people who need it faster. One method of achieving these goals is through closed connected single-use processing. Some of the advantages of closed processing include shorter processing time, fewer manual interactions throughout the process, decreased capital expenditures (CAPEX), reduced resources for cleaning and validation, and diminished footprints for qualified manufacturing space.
While closed connected processing offers advantages, it also requires new approaches with respect to process development, planning, and execution. Evaluation of new process methodologies is both time and resource consuming and can often be delayed or truncated. We performed an evaluation of biomanufacturing technologies, which can potentially improve efficiencies, and offer our findings as additional data for consideration when adopting these methods. The purpose of this discussion is to summarize our recommendations from our execution of a closed and connected mAb process from design considerations to scale-up, including the small-scale modeling that directed our process at manufacturing scale.
Get unlimited access to:
Enter your credentials below to log in. Not yet a member of Biosimilar Development? Subscribe today.