Pharma 4.0 Adoption Needs Cooperation — Here's How To Build It
A Conversation with Malcolm Jeffers, IAAE
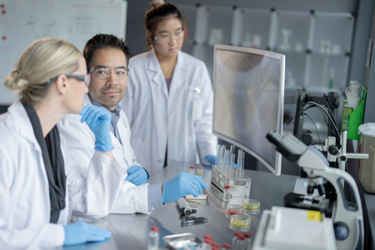
A recent survey by the International Society for Pharmaceutical Engineering (ISPE) found that an inadequate company culture raised the greatest barrier to digital maturity.
It wasn’t cost, technical know-how, or regulations. Instead, it was a lack of collaboration among departments to stitch together frontier information systems and equipment.
Malcolm Jeffers, transformation strategist at the International Academy of Automation Engineering (IAAE), spoke about the cultural bottlenecks and strategies for clearing them in December at the 2024 ISPE Pharma 4.0 and Annex 1 Conference.
We followed up with a few questions about building Pharma 4.0-ready teams. Here’s what he told us. His answers have been lightly edited.
We tend to think of Pharma 4.0 strictly in terms of new technology, but an ISPE survey found that culture quality, referring to values held by employees, is an increasingly relevant metric. Can you talk about that? How do you measure culture and how is it connected to Pharma 4.0?
Yes, ISPE Digital Transformation/Pharma 4.0 surveys conducted over the past three years have consistently revealed that a “non-adequate culture” is the greatest challenge to digital transformation listed by respondents, whether viewed by organization, by site, or by activity area (engineering and maintenance, manufacturing, and quality). Measuring culture can be challenging, but it typically involves assessing employee engagement, satisfaction, and alignment with organizational values. The ISPE Baseline Guide: Pharma 4.0 (First Edition) describes culture in chapter 5 as a “manifestation of people, processes, values, norms, and behaviors of the organization.”
Tools such as surveys, interviews, and focus groups can provide insights into the culture and themes that enable a particular cultural emphasis of an organization and several of these tools were used by the IAAE and research partners MIT and Digital Manufacturing Ireland in a recent study of manufacturers in Ireland. The findings of this study indicated that human-centric manufacturing culture is an enabler for accelerating digital technology adoption and innovation, a key goal of Pharma 4.0.
What are the IAAE-defined roles required to accelerate Pharma 4.0 within an organization?
Although not an exhaustive list, the following seven roles have been defined by the IAAE Life Sciences Advisory Board.
- Manufacturing leader: Owns P&L and proactively advocates for headcount and resources.
- Data steward: Advocates best data practices and ensures adherence to governance policies.
- Digital technology developer: Responsible for technology development and testing against business requirements.
- Digital technology owner: Leads development and implementation and improvement of specific technologies.
- Front line operator: Executes processes, works with equipment, generates and uses data.
- Change management lead: Creates strategy/framework for change and engages with stakeholders and users.
- Front line manager: Oversees operators and develops business requirements for technology needs.
It is important to underscore that collaboration between these roles is essential to achieve the desired outcomes of Pharma 4.0. The change management lead and manufacturing leader roles in particular have important “translator” benefits for the wider organization.
Also, as summarized in a recent article following an interview with leaders from Takeda and Fujifilm Diosynth, the activities of the data steward role, often carried out by people with different role names, are crucial for ensuring data quality and data governance, which are key aspects of Pharma 4.0.
Each organization will have its own naming approach, but readers may also find Appendix 5 of the recent ISPE Pharma 4.0 Baseline guide useful to refer to as it lists 11 example non-technical roles, with some overall to these roles pictured, for enabling a successful Pharma 4.0 implementation.
Does an organization need qualified people in each role for successful implementation? Can some people fill more than one role?
Without suitable people in place, organizations will likely struggle to identify and then realize the benefits of new technologies. So yes, having qualified individuals, including the roles we have defined, will be important for the successful implementation of Pharma 4.0. This said, Pharma 4.0 is not a “one and done” approach; it will require intentional investment in personnel skill development and knowledge management, just as it will require intentional technology investment.
In many cases, individuals may possess the skills and expertise to cover multiple roles, particularly in smaller organizations with limited resources. However, it is important to ensure that these individuals are not overburdened and that they have the support they need to perform their duties effectively. Cross-functional training and development programs can help build a versatile workforce capable of adapting to the evolving demands of Pharma 4.0. The activities required within the emerging role of data steward, as mentioned above, highlight the importance of a fluid resource model where team members have competencies in multiple data steward skills to enhance overall data governance.
Can you build structures to develop and sustain culture as you can for typical functions like unit operations?
Yes, and although difficult to achieve, this is certainly a goal of the organizations IAAE works with. As we listen to leaders who are quite sophisticated in their organizational change management practices, the structured initiatives they have put in place include:
- Change champion networks
- Communities of practice that support knowledge management
- Leadership development programs
- Employee recognition schemes
- Continuous improvement processes
When leaders foster a culture of learning and encourage and model cross-functional listening and collaboration, organizations can create and sustain an environment where employees feel valued and motivated to contribute to the success of Pharma 4.0 initiatives and the organization itself can better deliver on its objectives. By implementing such structured initiatives, organizations can create a culture that is good for the business and good for people, both workers and the patients they serve.
Briefly, can you explain how and in what areas the IAAE and ISPE overlap on Pharma 4.0 implementation?
The IAAE and the ISPE overlap in several key areas of knowledge and capability building. This is illustrated by the highlights overlaid on the ISPE Pharma 4.0 Operating Model pictured.
Slide presented at 2024 ISPE Pharma 4.0 and Annex 1 Conference, used with permission. Click for full size.
Both organizations emphasize the importance of automation and technical capabilities and encourage life sciences organizations to see digital maturity and data integrity by design as enablers within an industry that prioritizes quality and regulatory compliance.
The two organizations also share a commitment to the development and education of professionals either entering or already working within the industry, providing resources and training to engineers and others who engage with automation systems design or use.
Whereas the ISPE produces invaluable guidance documents, provides expansive training, as well as runs engaging conferences and webinars for its members, the IAAE has developed a library of industry vetted and credentialed education content, runs capability building programs with industry clients through learning sprints with subject matter experts on focused topics, and conducts research studies in collaboration with both industry and academic partners in the U.S. and Europe.
Additionally, and with a view to the future, both organizations are focused on developing the leaders of Pharma 4.0 transformations, the focus of a recent article with manufacturing leaders from Amgen, Lilly, and Vertex Pharmaceuticals.
About The Expert:
Malcolm Jeffers is the transformation strategist and head of research at the International Academy of Automation Engineering.