Single-Use Process Platforms Help Biomanufacturers Reduce Costs
By Miriam Monge
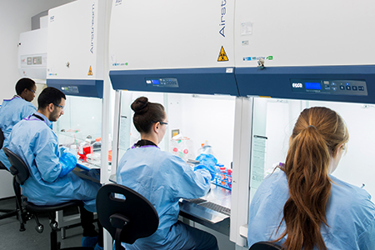
There are many new challenges facing those involved in the manufacture of biopharmaceuticals. Whereas in the past, overall process efficiency was sometimes treated as an afterthought as companies tried to get to market as quickly as possible, the production costs of biophar-maceuticals are now, receiving greater attention which is spurring interest in continuous bioprocessing. The loss of patent protection from blockbuster drugs is creating a market for biosimilars in which being able to compete effectively requires low prices underpinned by low manufacturing costs.
Enhanced flexibility and reduced operating costs are being achieved through the widespread adoption of single-use technology either as part of completely single-use processes or as hybrid solutions. However, questions around suitable stan-dards for product contact plastics continue to be debated within industry forums. Greater assurance can be provided to regulators that products are manufactured by well controlled and characterized processes due to advances in process analytical technologies and enhanced QbD regulatory submissions.
While bioprocess engineers must now apply themselves to addressing these issues they can at least be thankful that the collective experience within the industry is now sufficiently great that many of the original challenges faced by teams in the first few decade of the industry have now been resolved. Unless a particular project requires the entire process to be reimagined there need be no reason for designing individual bioprocesses from scratch. Fortunately we are able to stand on the shoulders of bioprocessing giants.
Platform processes that are capable of being used to manufacture different biologics from the same class are arguably the physical embodiment of this collective knowhow. The platform approach can be applied to classes of biopharmaceuticals such as Monoclonal Antibodies, Antibody-Drug Conjugates and Vaccines. Process platforms allow tremendous efficiencies to be gained as they utilize the same equipment, supply chain for consumables, documentation and training. Learning acquired from the operation of one process can be applied to other processes within the platform and data can sometimes even be shared between processes during regulatory submissions.
For these reasons companies that have a pipeline of similar molecules have adopted the process platform approach to increase the efficiency of process development and increase standardization within operations. Contract Manufactur-ing Organizations often make great use of process platforms because of their need to perform rapid process transfers and operate many different processes. Cost and time savings can be gained wherever it is possible use common equipment, methods and raw materials.
In this era in which organizations can be virtual and often increasingly without borders, a new trend is emerging whereby biopharmaceutical companies are collaborating with capable suppliers who can provide entire platform bioprocesses to their partners. Based upon the supplier’s experience of working on many develop-ment and engineering projects with multiple clients their accumulated exper-tise can be leveraged by biopharmaceuti-cal companies seeking to rapidly install new production capabilities. These may be smaller companies whose focus has previ-ously been on drug development but wish to develop a manufacturing competency or larger companies that want to outsource bioprocess innovation to a partner.