5 Strategic Advantages Of Manufacturing ADCs In-house
By Mei-Chun Yang, CEO, GlycoNex
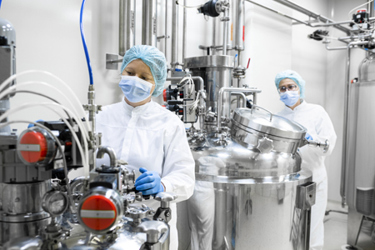
In the competitive landscape of biotechnology, particularly within the rapidly advancing antibody-drug conjugate (ADC) sector, the pressure to innovate and bring products to market efficiently has never been greater.
As the demand for more targeted and effective therapies grows, companies must navigate complex regulatory environments, manage intricate supply chains, and meet stringent quality standards. In-house manufacturing, coupled with full capabilities in antibody optimization, functional evaluation, and process development, has emerged as a critical strategic approach that enables biotechnology companies to maintain control over every aspect of the development process.
This level of control allows companies to not only ensure the highest standards of quality but also to drive down costs, streamline operations, and respond swiftly to market demands.
Success in manufacturing advanced biologics, such as ADCs and bispecific antibodies, requires a deep level of customization and meticulous oversight — both of which can be managed through an in-house manufacturing model. By adopting in-house capabilities in antibody development and manufacturing, biotechnology firms can establish a foundation for long-term success by building on the following advantages.
Enhanced Control And Quality Assurance
One of the most significant benefits of in-house manufacturing is the enhanced control it provides over the entire production process. For GlycoNex, which specializes in glycan-directed ADCs and biosimilars, in-house manufacturing is a strategic approach that has proven highly beneficial.
To predictably produce glycan-directed ADCs of consistent quality – which offer the potential to target multiple glycoproteins across different types of cancer cells for better treatment outcomes — expertise, flexibility, and quality assurance are paramount. This direct oversight ensures that all manufacturing stages adhere to rigorous quality standards, resulting in reliable products. In the context of ADCs — particularly glycan-directed ADCs, which have the potential to bypass certain cancer resistance mechanisms and avoid some common resistance mechanisms associated with protein-targeting therapies. Precision and consistency are essential.
With in-house manufacturing, companies can promptly address any quality issues, implement improvements, and ensure that their products meet the stringent requirements of clinical and commercial markets, especially when dealing with the unique challenges of novel targets like glycans.
Cost Efficiency And Operational Streamlining
Cost efficiency is another critical advantage of in-house manufacturing. By reducing reliance on third-party manufacturers, companies can significantly cut down on outsourcing costs. This internal approach not only saves money but also streamlines operations, improving coordination and reducing delays. Additionally, it mitigates the risks associated with unpredictable global supply chains, which are increasingly vulnerable to geopolitical disruptions. For companies that specialize in glycan-directed ADCs, in-house manufacturing allows them to manage internally the complex and costly process of producing high-quality antibodies that serve as the foundation for these therapies. This control over the entire production process helps drive down the overall cost of development. This ability to control the entire process is crucial for optimizing the development of glycan-directed ADCs, ensuring that these innovative therapies can be produced efficiently and effectively.
Accelerated Development Cycles And Increased Agility
In-house manufacturing capabilities enable biotechnology firms to accelerate their development cycles and increase their operational agility. With complete control over production, companies can quickly iterate and make necessary adjustments without the delays associated with external partners.
For smaller biotech companies, in-house manufacturing also means they don’t have to compete for manufacturing capacity at contract development and manufacturing organizations (CDMOs), which often prioritize larger, higher-paying clients. This dynamic can lead to significant delays that disrupt clinical trial planning and progress. By avoiding these external dependencies, even small companies working to develop advanced biologics can accelerate the development of next-generation targeted therapies like glycan-directed ADCs.
Intellectual Property Protection And Innovation
Protecting intellectual property (IP) is a top priority for biotechnology companies. In-house manufacturing plays a vital role in safeguarding proprietary information by minimizing the risk of IP leaks or breaches. When sensitive processes are handled internally, companies can better secure their innovations and maintain a competitive advantage. Moreover, in-house capabilities foster innovation through close integration of development stages and cross-functional collaboration.
Seamless transitions between stages encourage creativity and lead to more comprehensive and effective development strategies.
Scalability, Protocol Modification, And Talent Retention
Scalability and flexibility are essential for biotechnology firms looking to adapt to market demands. In-house manufacturing allows companies to scale up processes efficiently and modify protocols as needed, ensuring that production can meet both current and future needs. This capability is particularly important in optimizing the complex processes involved in glycan-directed ADC development, which require careful consideration of scalability from the outset.
The dynamics of a flexible and scalable company attract and retain top talent, providing employees with opportunities to work on cutting-edge projects that cultivate a diverse skillset and foster a strong sense of progress and achievement. A skilled and motivated workforce is a significant asset, driving continuous improvement and innovation.
Manufacturing The Future And Building A Competitive Edge
The strategic advantages of in-house manufacturing for ADC development are clear. Enhanced control and quality assurance, cost efficiency, accelerated development cycles, IP protection, and scalability collectively contribute to a biotechnology firm's success.
These advantages are crucial in advancing our glycan-directed ADCs and biosimilars. By investing in these capabilities, companies can not only improve their operational efficiency but also ensure that they remain at the forefront of innovation in the development of advanced biologics. As the ADC space continues to evolve, the adoption of in-house manufacturing will undoubtedly play a crucial role in shaping the future of ADC development and beyond.
About The Author:
Mei-Chun Yang is the CEO of GlycoNex, a biotechnology company specializing in glycan-directed cancer therapies. With over 20 years of experience, she drives innovation in antibody-drug conjugates, advancing targeted treatments that improve patient outcomes g