Safety Cabinets' Essential Role In EU GMP Annex 1
By Andreas Nuhn, GMP Compliance Adviser
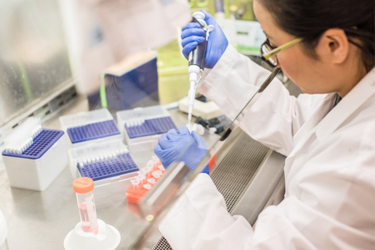
Safety workbenches offer product protection in the smallest of spaces and personal protection without the need for protective clothing. There are three types of safety workbenches, which offer either product protection only or product and personal protection. Depending on the requirements, clean workbenches are used, for example, for sterility tests, biosafety cabinets for working with microorganisms or cytostatic workbenches for the preparation of CMR preparations.
What Is The Purpose Of Safety Cabinets?
Cleanrooms are used for protecting products against contamination. The focus is on avoiding contamination by particles or microorganisms. In some cases, however, not only the product has to be protected against contamination, but the environment and the employees have to be protected against the product as well.
This applies, for example, when working with:
- biological materials, i.e., microorganisms that are infectious, toxic, or have human allergenic potential,
- CMR materials (carcinogenic, mutagenic and toxic for reproduction), e.g., cytostatic, monoclonal antibodies, and virostatic agents), and
- HPD materials (highly potent drugs), which have a pharmacological effect even at very low doses.
In order to avoid the necessity of full protection equipment and/or limit the cleanroom zone required to a minimum, safety cabinets are often used in such cases.
There are three different types of cabinets available, which are described below:
- Clean benches
- Biosafety cabinets (Class I-III)
- Cytostatic safety cabinets
Classification Of Cabinets According To Annex 1 Of The EU GMP Guidelines
If safety cabinets are used in pharmaceutical sterile production, the work area of the cabinet must comply with cleanroom class A requirements. When classifying the work area inside the cabinet, it is important to note that an air velocity of 0.45 m/s ± 20% (0.36 m/s to 0.54 m/s) is required to achieve cleanroom class A in accordance with EU GMP Guide Annex 1. A speed with a corresponding distance to the lower permissible limit is easily achieved today by most manufacturers of such workbenches, provided the requirement is known when the order is placed.
If safety cabinets are used in laboratories (i.e., outside of pharmaceutical production), the requirements described regarding velocities do not apply. Such safety cabinets are designed for slightly lower air velocities. This results from the specification in EN ISO 14644-4, where a flow rate of only 0.2 to 0.5 m/s is stipulated for a low-turbulence laminar flow.
Clean Benches
Clean benches only protect the product. A low-turbulence laminar flow (LF) (vertical or horizontal) inside the bench protects the product against external influences. This type of cabinet is frequently used in the pharmaceutical industry for sample-taking, i.e., when only a small cleanroom zone is necessary and only product protection is required. Such workbenches are not used in the production area, but are used in the incoming goods department, for example.
This type of cabinet normally has a straightforward design. It consists of a housing usually made of powder-coated sheet metal. The fan sucks the air from the room through a pre-filter and then blows it through a HEPA filter (Class H13 or H14) toward the product and at the operator. This type of cabinet is commonly referred to as a "clean bench" or "LF box".
As users are usually unable to distinguish between clean workbenches with a vertical airflow and biosafety workbenches, a warning should be displayed stating that this workbench only provides product protection.
Biosafety Cabinets (BSC)
Depending on the design or classification of a biosafety cabinet, it provides personnel protection only or personnel and product protection.
In accordance with EN 12469, biosafety cabinets can be divided into three classes, which are described below.
Biosafety Cabinets Class I
Class I BSCs only provide personnel protection. Air is drawn from the room through the work aperture across the work surface. If particles or aerosols are released when work is being carried out, they are transported to the exhaust air filter (normally a HEPA filter). As a result, the environment is protected against any substance that is processed inside the cabinet.
This protection can be maintained as long as the airflow is not hampered or interrupted (e.g., by placing large pieces of equipment directly behind the work aperture) and as long as the air volume entering the system is large enough to transport particles.
These cabinets are mainly used in biological laboratories when product protection is not necessary, e.g., when evaluating microbiological samples that are subsequently destroyed. Class I cabinets may only be used in laboratories of protection class S3 in accordance with EN 12128.
A class I BSC is not the same as a laboratory fume hood, often found in chemical laboratories. The objectives are identical, but the design and safety requirements are different.
Biosafety Cabinets Class II
Class II BSCs are used both for product protection and personal protection. These are the most common cabinets used in biological and pharmaceutical laboratories.
Areas Of Application
Biosafety cabinets with GMP requirements are primarily used in the manufacture of sterile medicinal products - usually in patient-specific production (compounding). Another important area of application is sterile testing.
Nowadays, isolators or class III BSCs are used in some situations instead of class II BSCs or cytostatic safety cabinets.
Class II BSCs that are used to produce CMR materials are generally referred to as cytostatic safety cabinets. They have an additional third filter and must meet the requirements of DIN 12980. Devices used for microbiological or biotechnological work must comply with EN 12469. Both standards are very similar with regard to safety requirements and their tests.
Air Conduct
In Class II biosafety cabinets, air is drawn in from the room via the front intake opening and forms an air curtain for personal protection. Inside the workbench, a vertical laminar downflow is generated via the main filter (blue) from top to bottom to the extraction openings located at the edges of the work surface. The downflow ensures product protection. Approximately 70% of the airflow is circulated; the remaining 30% is released back into the room via HEPA filters and is thus in balance with the 30% of the air from the room that is sucked back in via the front intake opening.
A balance between downflow and inflow is necessary to ensure effective protection. Some manufacturers and users reduce the downflow (e.g., to reduce energy costs, prolong the filter service life, or with the aim of installing smaller and cheaper fans). This leads to a simultaneous reduction in inflow and, as a consequence, to a reduced level of protection for the operator.
Protection is only maintained as long as the airflow is not hampered). Disturbance of the laminar airflow can quickly lead to turbulence that releases aerosol-containing air from the work zone, putting personnel at risk.
Personal Protection
Proof of personal protection is also provided by the so-called KI discus test in accordance with EN 12469, in which the retention capacity at the working opening is checked. This test is particularly necessary during commissioning, recommissioning, repairs, or other changes to the ventilation technology.
It is also important to remember that the operator's hands and arms are not protected by the cabinet. This requires the use of suitable personal protective equipment.
Construction
The height-adjustable front panel is used for controlling the airflow. The aperture is reduced to a minimum working size, normally about 250 mm to 300 mm. This ensures that the velocity of the inflow remains high. The aperture should be kept closed outside working hours to prevent contamination of the cabinet from the environment when the airflow is switched off. The aperture can be increased during cleaning and servicing to make it easier for the operator to carry out that kind of work. The workbenches currently available on the market generally have glass panels. The front panels of some older cabinets are made of plastic; the panels of later models are normally made of glass. As plastic panes can become blind in the long term due to the regular use of disinfectants, some of which are aggressive, care should be taken to ensure that the front and side panels are made of glass when purchasing new units.
The work surface is made of stainless steel to ensure resistance against all common cleaning and disinfection agents. Contamination frequently occurs below the actual work surface because of the front and rear suction vents. To enable the area under the worktop to be cleaned, the worktop is usually divided into individual panels. These can be easily removed or moved to clean the area underneath.
Liquid leaking through the gaps between the individual segments can, depending on the shape of the individual segments, also lead to contamination in the space below the work surface. In many cases, this is now prevented by appropriate upstands in the areas between the individual panels. This space must be regularly cleaned and disinfected when aseptic production is being carried out, regardless of obvious contamination. For this reason, plates with holes in the work surface should not be used for aseptic production processes in the workbench, as they are much more difficult to keep clean, even if they have a positive effect on the uniform airflow.
Filter System
Class II BSCs are available with a two or three-filter system. Three-filter systems protect against the particulate contamination of areas that are difficult to access, e.g., the interior space of the air return in the cabinet. EN 12469 also stipulates that air channels that may retain contaminated air should be kept as short as possible. This filter also removes a high percentage of particles from the air. The downstream filters are exposed to air that is practically free of particles, leading to a much longer service life.
The third filter (the first filter in the direction of the airflow, frequently referred to as the first filter or first filter stage) is normally installed at the rear of the cabinet above the footwell. It is normally easy to recognize these cabinets by the slope below their work surface.
Biosafety Cabinets Class III
The class III BSC is a closed system under negative pressure. In terms of design and use, this BSC corresponds to an isolator. Work is carried out with permanently fitted gloves, and materials are introduced and removed exclusively via airlocks in which appropriate decontamination takes place. The HEPA-filtered supply and exhaust air is regulated in such a way that the negative pressure in the workbench is maintained during all work steps.
The advantage of this system is the high level of user protection, as there is a physical separation between the operator and the product, and the separation is not just via an air curtain as with class II BSCs.
Disadvantages are the rather complex handling of the materials to be introduced due to the airlocks and the cumbersome work due to the rather thick-walled, permanently installed gloves.
Cytostatic Safety Cabinets
The requirements outlined below must be met when cytostatics are prepared. However, they also apply to other substances, e.g., other CMR substances, genetically modified organisms, and microbiological organisms in the biosafety level (BSL) 2-4 risk categories.
Cytostatic workbenches must comply with DIN 12980. This is a purely German standard but has been adopted by most European countries.
Installation
When one or more safety cabinets are installed in a room, they must not be allowed to have a negative effect on their respective protective function or on that of other cabinets in the room. The Quality Standard for Pharmaceutical Oncology Services of the European Society of Oncology Pharmacy contains the following general requirements for the room in which a workbench is to be set up:
- Size of room: min. 10 m2
- Height of room: min 2.5 m
- Free movement area at the workplace: not less than 1.5 m2 and not less than 1 m wide at any point.
- Minimum clearances: no furniture, appliances or walls may be located 1.2 m behind and 0.3 m to the side of the workbench
It has been proven that people walking past the front of the cabinet have the greatest impact on the protective function of the cabinet. For this reason, particular activities should be refrained from in the room when critical work steps are being carried out. The protective function is also impacted by the user moving his/her arms.
Connecting To The Ventilation System
When safety cabinets are used during the processing of substances that are hazardous to health, the exhaust air must never be returned to the room (personal protection!). Safety cabinets that cannot be directly connected to the exhaust system are an exception. In such cases, the exhaust air must be filtered twice using H13 or H14 filters. At the same time, it must be proven that materials from the safety cabinet cannot escape into the surrounding room. For this reason, it is important to ensure that newly installed safety cabinets can be connected to the exhaust air system.
Figure 1: Open connection of a cytostatic safety cabinet
Experience has shown that the exhaust fan performance of central air-handling systems tends to fluctuate; as a result, a permanent connection is not advisable. An increase in the volume of extracted air can mean that the product is no longer protected. A decrease in the air volume can lead to back pressure in the cabinet, with the result that the protection of personnel can no longer be maintained. For this reason, an open connection (connection with draft interruption) is usually selected instead of a fixed connection, in which the differential air volume is extracted from the room. The two vent pipes are aligned centrally in one another, leaving a gap through which the balance of air can be sucked in (see Figure 1).
This article is an excerpt from GMP knowledge contained in the online portal GMP Compliance Adviser, which provides in-depth information about GMP best practices and regulations with a focus on Europe, but also referring to the U.S., Japan, and many more (PIC/S, ICH, WHO, etc.).
Editor's note: The text has been updated to reflect the correct air velocity range recommended by Annex 1 for class A cleanrooms. The correct range is 0.36 m/s to 0.54 m/s.
About The Author:
Andreas Nuhn has been working as a freelance consultant since 2013. He uses his experience in GMP compliance projects when preparing FDA audits and at various training events. His areas of expertise include cleanroom planning and operation as well as the operation of isolators. After graduating in process engineering and biotechnology, he quickly moved into the area of GMP compliance in companies. He worked as a project manager for different pharmaceutical manufacturers and manufacturers of medical products in Germany and abroad.