Samsung Bioepis: Turning "Lessons Learned" Into Biosimilars

By Anna Rose Welch, Editorial & Community Director, Advancing RNA
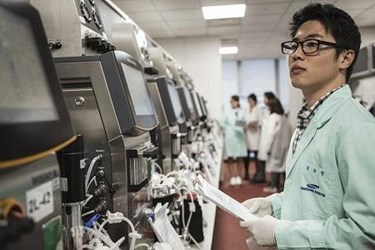
In the first part of this two-part article, Paul Song, VP at Samsung Bioepis, highlighted the company’s “process innovation.” The integration of Quality by Design (QbD), Failure Mode Effects Analysis (FMEA), Agile, and Toll Gates into the traditional biosimilar development process has helped the five-year old company achieve leadership in the European biosimilar market.
In fact, over the past five years, “process innovation” has become the company’s mantra. It applies to all aspects of performance, whether it be drug development or managing the laboratory, finances, or public relations. But in order to get its pipeline before regulators all within five years, Song emphasized the importance of “lessons learned.”
“It took a while for [QbD, FMEA, Agile, and Toll Gates] to be fully embedded in our development process,” explained Song. “But over time, we’ve learned new things, and, in turn, this new knowledge has been integrated and implemented into the process. These ‘lessons learned’ are taken very seriously as part of the standard operating procedures [SOPs] at Samsung Bioepis.”
In the pharmaceutical industry, five years is a short length of time in which to launch a company, establish a development process, and bring several candidates to market. In our interview, Song shared some of the efforts the company has made to pass down lessons learned and to continue evolving in the years ahead.
Challenges Of Implementing Process Innovation
At Samsung Bioepis, as at any company, SOPs are regularly evolving, and, as such, require a great deal of documentation and training. “This is a very dynamic process,” Song qualified. “It’s a combination of four elements [QbD, FMEA, Agile, and Toll Gates] that are put together into one in our standard operating procedures (SOPs).” New knowledge — for instance, new or improved operational methods, analytical tools, or assay protocols — is regularly added and needs to be communicated to new and regular employees.
These lessons are integrated into a company-wide project management program, so that the information can be tracked and efficiently shared among all employees. This is especially important for a growing company, like Samsung Bioepis, since assignments might be switched from one person to another as new hires come in. The company currently comprises approximately 700 employees, a majority of which are some of the youngest in the entire Samsung enterprise. The average employee age at Samsung Bioepis is 32.
Rigorous training programs have been a particularly important part of the company’s culture. These training programs have been key for imparting new lessons learned.
Inspiring confidence in new procedures is a challenge any company faces. For example, Song homed in on the work it took to integrate FMEA into Samsung Bioepis’ development process. Not only did the purpose and goal of FMEA need to be emphasized, but employees also needed to learn and accept that the process required a lot of upfront work.
“FMEA requires us to build a very detailed process map before we even start a single experiment,” Song described. “Though we do use prior knowledge, we need to establish diverse scenarios of the problems that may occur so that we have a very effective risk management plan in place.”
Song explained this process to me using cooking ramen noodles as an example. You begin by making a list of the steps it takes to make ramen noodles (roughly 10 to 15 steps). You then consider all the potential problems (or scenarios) that might arise during the cooking process. FMEA provides a Risk Priority Number (RPN) score, which quantifies potential risks. The RPN reveals how severe each risk will be, how likely it could occur, and how easily it can be detected. “The higher the score, the larger the risk, which means a company will need to establish a more thorough mitigation plan,” Song emphasized.
While some employees might be concerned about spending lots of time planning prior to action, Song emphasized that a mistake happening later in the development process will end up being more costly than all the upfront work.
Looking 10 years down the road, Song expects Samsung Bioepis will continue to refine its processes in order to push for higher quality and fewer failures — though he added “we’ve been very, very fortunate at not having had any major failures.” One of the ways the company can attain a higher quality is by improving cell lines to yield higher titers. But doing so will also help lower the cost of goods, which is another way Song feels the company will continue to evolve.
“We continue using this process so that we can reduce the development costs, because, at the end of the day, any reduction in cost will help us and our biosimilars reach more patients,” he said.